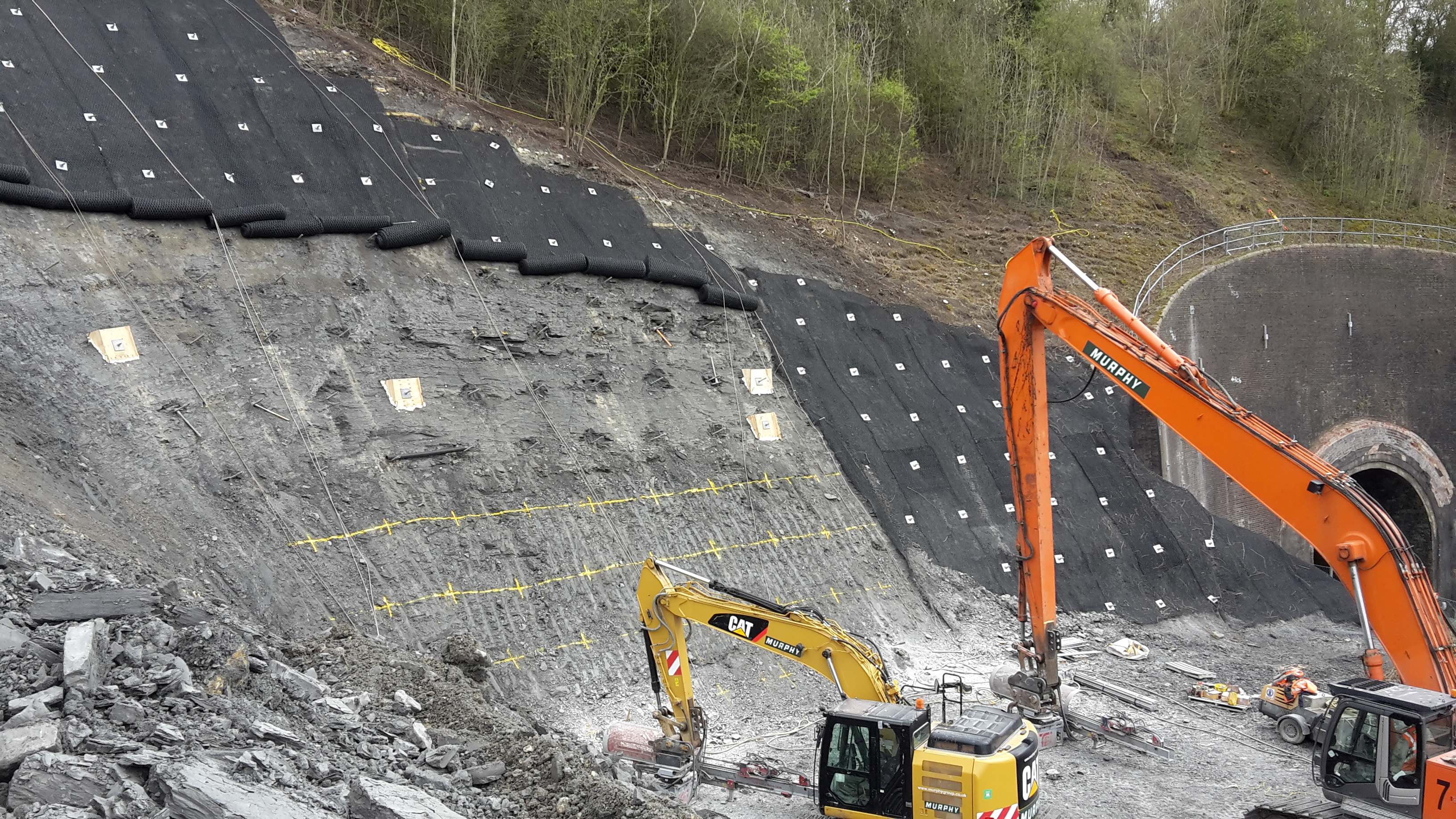
Harbury Cutting
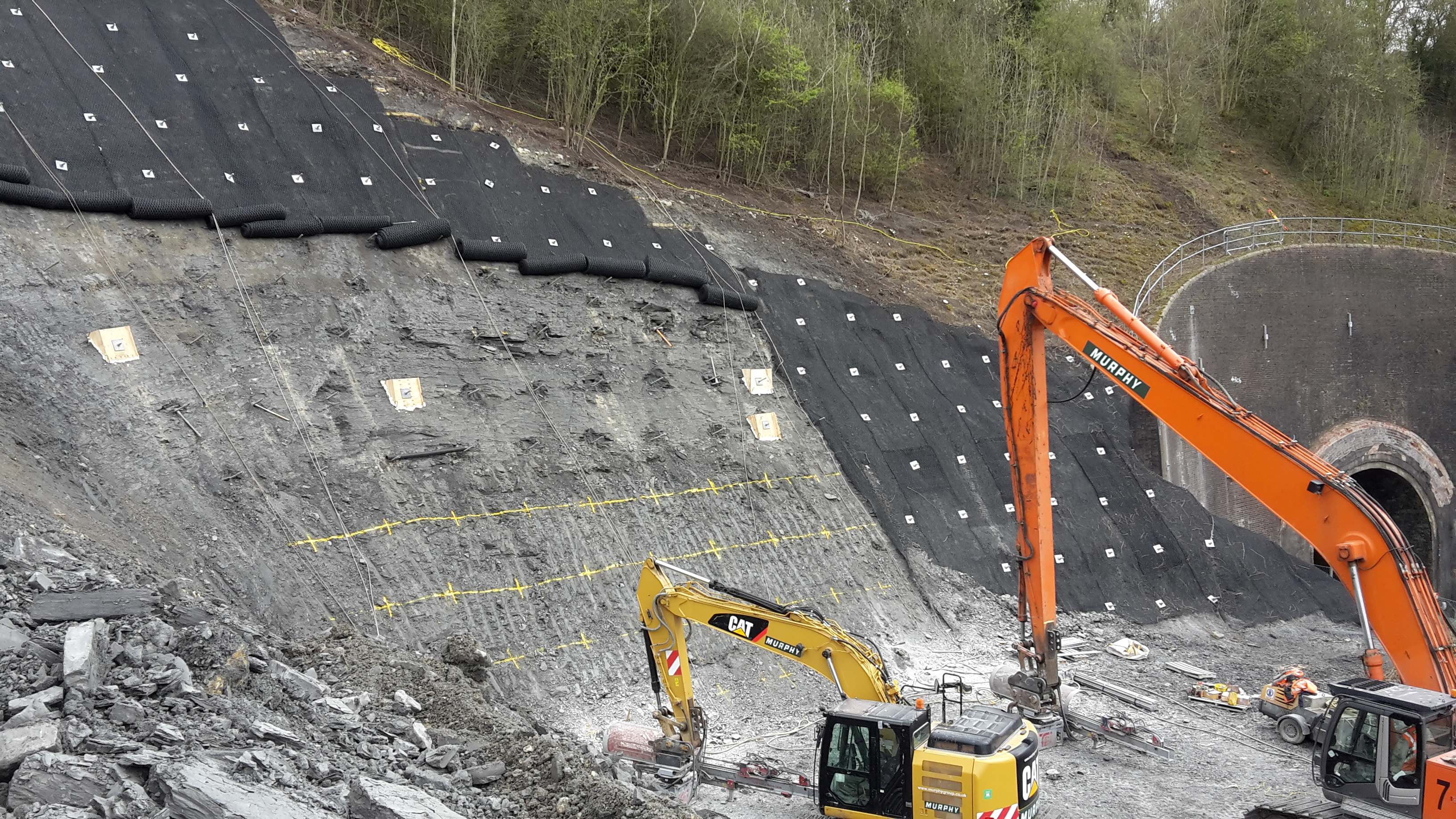
The Scope
Harbury Cutting was constructed in the 1840s by Brunel and at 34m deep is recognised as the largest hand dug rail cutting in the world. The cutting had a history of geotechnical failures, which led to a major disaster where the embankment crest dropped by 4m and over 300,000 tonnes of material slid towards the track. The landslide took away part of the west portal which is a curved mass brickwork structure over 50m wide and 15m high.
The Challenge
During ongoing works on a minor slip, Vertical Access Ltd was requested to install a 290-meter catch fence which successfully limited the movement of a landslide, preventing it from affecting the active railway track. When the major landslip occurred, an emergency plan was instigated to stabilise the cutting and portal. We were brought in to perform soil nailing on the slope adjacent to the portal and to install anchors through the portal to prevent further collapse.
The Vertical Approach: Safety, Quality, Innovation & Agility
Safety
Safety was a critical concern due to the continuously moving slope, which required constant monitoring to protect the operatives working on the slopes and structures. The presence of water jets during trial drilling highlighted the complex and hazardous conditions, necessitating rigorous safety protocols and continuous alert systems to ensure the well-being of all personnel on site.
Quality
Quality control was paramount in addressing the unstable ground conditions. The evolving design, influenced by real-time feedback from trial works, included the use of sulphate-resisting grout to enhance durability. The precision required for diamond coring through 2-metre-thick brickwork and the installation of soil nails and support-plates demanded meticulous attention to detail, ensuring the stabilisation efforts met the highest standards.
Innovation
Innovation was key to overcoming the project's challenges. The discovery of a vertical fault line of limestone necessitated adaptive strategies. Vertical Access utilised large excavators up to 67 tons, fitted with TEI drill rigs and masts, to handle the 20-meter long soil nails. The design of a custom platform supported by Mabey System 160 brackets and rope access systems for brick re-casing demonstrated ingenuity in providing a safe and effective solution for the complex stabilisation tasks.
Agility
The project required exceptional agility in mobilising resources, plant, and materials under tight deadlines. Network Rail's commitment to reopening the railway within nine weeks demanded 24/7 operations. VA coordinated a diverse team drawn from sites across the UK, working in a rolling program to drill and mesh, ensuring timely completion. The ability to adapt to evolving ground conditions and collaborate effectively with Murphy for the safe and efficient operation of excavators, dumpers, drilling plant, and rope access personnel was crucial to meeting the project’s stringent timeline.
Outcome & Feedback:
VA’s comprehensive approach to safety, quality, innovation, and agility ensured the successful stabilisation of the landslip area. The installation of soil nails, the support of the brick portal, and the completion of all tasks within the tight schedule allowed the railway to reopen on March 13th, 2015, ahead of the planned deadline. The project exemplifies effective emergency response and engineering excellence in challenging conditions and was even commended by Mark Carne (Chief Executive of Network Rail)
TESTIMONIAL
“Thousands of passengers, and thousands of tonnes of freight, rely on this vital route every day. We have been working around the clock and are able to reopen the railway three weeks ahead of the original estimate.
Mark Carne
Chief Exective, Network Rail